Over time, CIVE® has gained dynamic experience in the construction industry and is always keen to share it with those who need it - owners, clients, potential investors, architects, engineers and other industry professionals. CIVE® Resources is a well-rounded source of industry specific knowledge base that acts as a guide in varying trades of the industry.
Resources
Blogs
Our guides act as a valuable resource and covers a range from basic construction process to specific concerns in different types of buildings. These E-books will help guide you whether you're in search of investment options for a project or looking to expedite ways of project deliveries.
Whitepapers
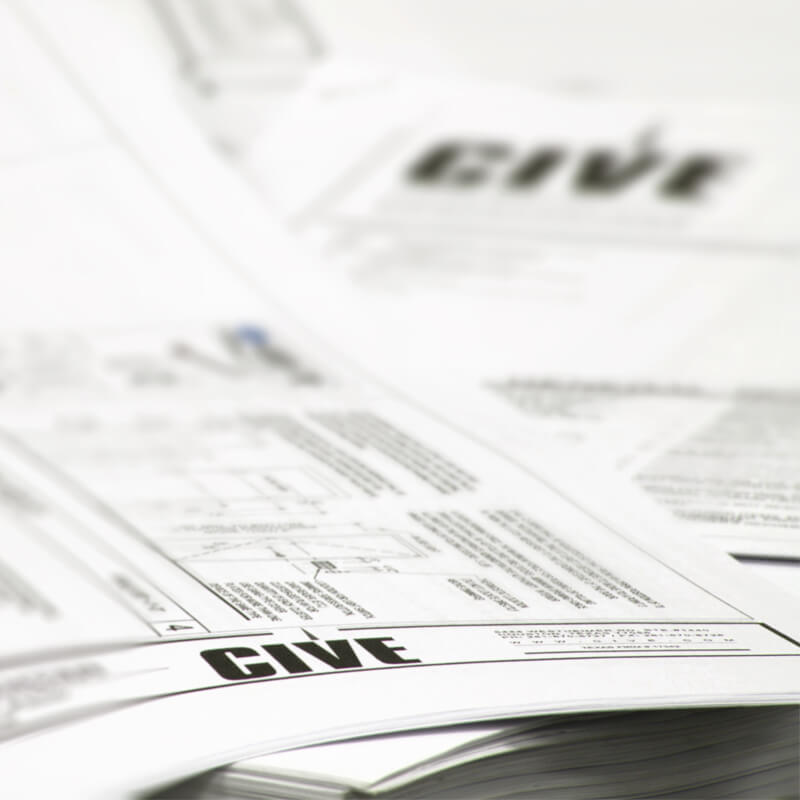
Phase 1: The Pre-Construction Phase
The Pre-Construction Phase
The pre-construction phase is the beginning of the construction process and is a crucial part of any construction project.
Key Steps in the Pre-Construction Phase
During this phase, planning and design occur. The importance of careful planning and designing cannot be overstated as it can minimize delays and according to Gambatese et al. maximize worker safety. “Designing for construction safety entails addressing the safety of construction workers in the design of the permanent features of a project.” The steps involved in the pre-construction phase are as follows –
- Conceptualization, Design, and Feasibility Analysis
- Obtaining Permits
- Cost Estimation
- General Contractor Selection
- Material Procurement
- Secure Funding
Conceptualization, Design, and Feasibility Analysis
In order to begin the full-scale design process, a feasibility analysis, or feasibility study, should be performed. Often before the primary feasibility study can be conducted, a preliminary feasibility study is completed. A preliminary feasibility study, or pre-feasibility study “helps to “frame” and “flesh-out” specific business scenarios” (Iowa State University 2020) or, in terms of construction, helps to narrow down the list of potential projects. Following the preliminary feasibility study, the primary feasibility study is conducted. Feasibility studies are conducted by project coordinators to “determine the viability of their idea before proceeding and incurring upfront development costs” (Iowa State University 2020)’. Feasibility studies are also used to identify issues with the project or project site that need remedying and conduct environmental impact assessments (EIA).
Before there can be a structure, there must first be an idea. Many construction projects begin with a “needs assessment”. A needs assessment is the process by which the purpose, or function, of a construction project is identified. Need assessments can come in several forms. Even when someone looks in the refrigerator to determine what they need to cook a meal, they are performing a needs assessment. In the context of construction for example, a landowner looking to develop their property can perform a rudimentary needs assessment to determine what type of structure would be most successful at that location, or a skilled laborer looking to open a business front may complete a needs assessment to identify where their business would earn the most profit or contribute the most to the surrounding community. This process can also include establishing the basics of construction design and necessary facilities.
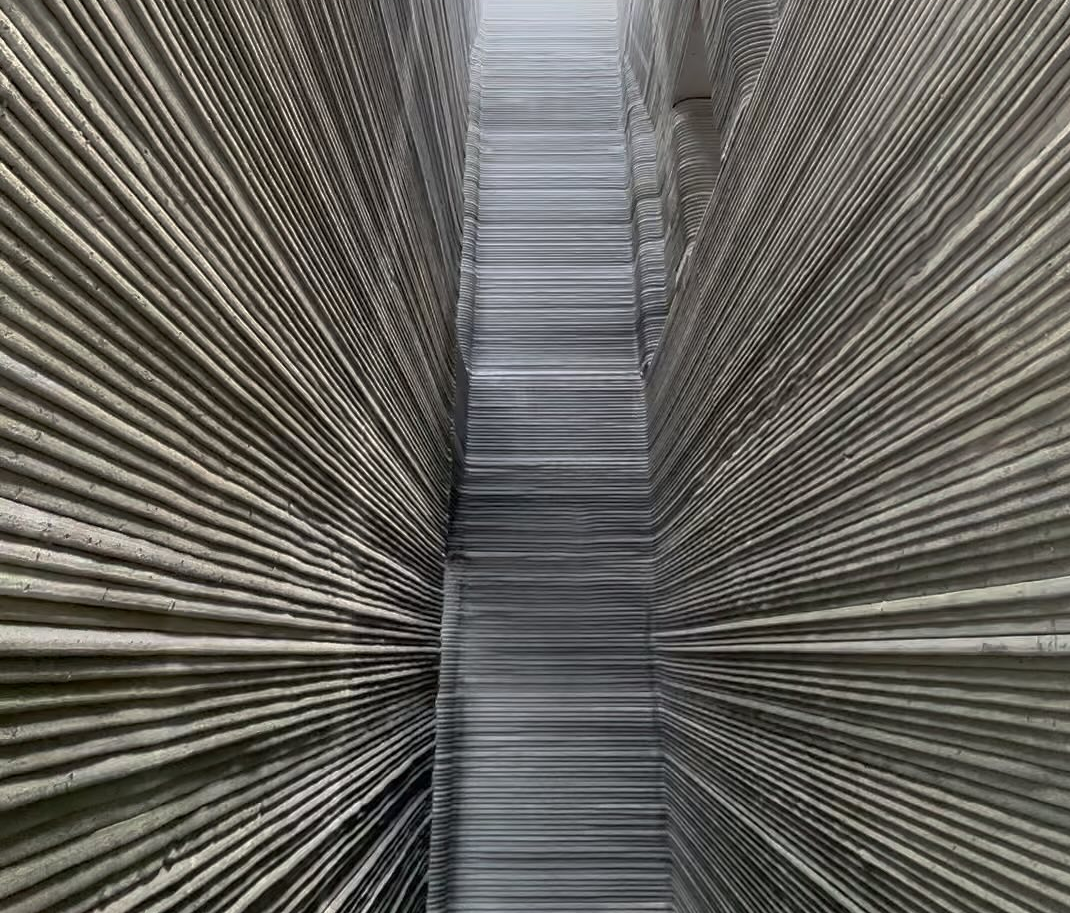
Case Study: Precast Concrete Walls vs Traditional Concrete Tilt-Up Walls vs 3D Printed Concrete Walls
Precast Concrete Wall Panels
Precast concrete wall panels, also referred to as prefabricated concrete walls, are concrete wall panels engineered and manufactured almost entirely in a controlled factory environment before being transported to the construction site. Sometimes called plant-cast concrete wall panels, these concrete walls are designed to be strong, durable, and versatile.
Materials – Composition
Prefabricated concrete wall panels are made from a variety of materials. The ratio of materials can differ based on desire strength, durability, and aesthetic appeal. The main material used in precast concrete walls is, of course, concrete. Made by mixing cement, water, aggregate (sand, gravel, or crushed rock), and sometimes admixtures, the concrete is then poured into a mold to achieve the desired shape and size.
These concrete panels are often reinforced to increase the wall’s strength and durability. The reinforcement is typically placed inside the concrete before it hardens, and it helps the concrete to resist tensile forces, which are forces that tend to pull things apart. This reinforcement can come in many forms including but not limited to prestressing materials, deformed bars, and welded wire fabric.
The precast concrete wall panels can be insulated for energy efficiency. This is achieved using materials like expanded polystyrene (EPS), extruded polystyrene (XPS), or polyurethane foam. Insulation can give precast concrete walls a high effective R value. The higher the R value, the better a material is at resisting heat flow, therefore, the higher a material’s R value, the greater its insulation properties. Unlike the standard R-value, effective R-value includes the cumulative effect of all the materials used in the construction of a particular element of a structure when determining the thermal resistance of a construction material.
Labor – Quantity, and Type
The manufacturing and installation of precast concrete wall panels is done in several steps, each requiring different types of labor. This begins with skilled engineers and architects who design the precast concrete wall panels according to the specifications of the project. Then, after these designs are approved, they are sent off to be manufactured. The manufacturing process requires a variety of people including production workers, quality control technicians, supervisors and equipment operators. After design and production, the precast concrete wall panel must be transported to the construction site. This means truck drivers and logistic personnel must be employed. Following transportation, construction workers, such as crane operators, site supervisors, projects managers, safety personnel, and others are needed to complete installation. The exact number of laborers needed in each category will depend on the scale of the project, the complexity of the designs, the size and number of panels being manufactured and installed, and the efficiency of the equipment and processes used.
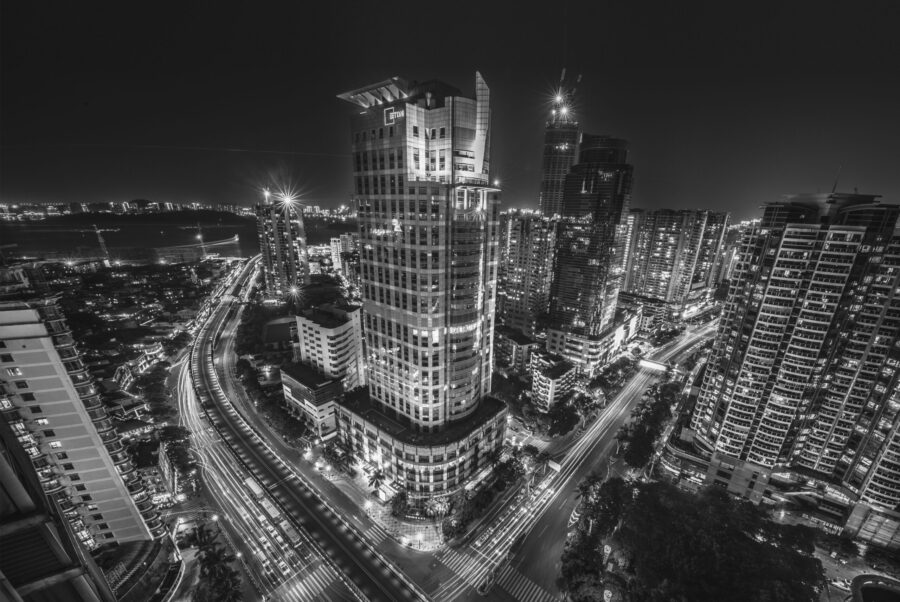
Structural Engineering: Elements of Every Structure
Structural engineering elements are the pieces that compose the “skeleton” of structures. Just like the bones of the human body, the skeleton of a building provides strength, shape, and stability. These elements come in various shapes and sizes and similar to other sciences, form follows function. This paper explains the importance and roles of the very basic structural elements such as beams, columns, and foundations. These work together along with various other elements to create a strong, stable, skeleton for buildings and structures.
Beams
A beam is a load-bearing, horizontal, straight member that has high flexural strength. Flexural strength refers to the load-bearing capability of a material or structural element. Structural elements with high flexural strengths can undergo immense bending stress without deformation or yielding. Beams are often categorized by the way they are supported. Examples of this include simply supported beams, cantilevered beams, continuous beams, and fixed supported beams.
A simply supported beam is a beam that rests on two supports with inhibited vertical movement. This is because simply supported beams have one “roller support” and one “pinned support”. A roller support is a support that is free to move both horizontally and rotationally but not vertically. Contrastingly, a pinned support, also referred to as a hinge support, is a support that cannot resist movement. A pinned support allows the structural element to rotate, but resists both horizontal and vertical movement. These beams are commonly used in bridges, and are easy to install. Although easy to design and effective, simply supported beams have disadvantages. Compared to fixed beams, simply supported beams have reduced ability to resist bending loads.
Cantilevered beams are horizontal, and only have one end support. These beams are often used in buildings to support things such as eaves and roofs. Like other beams, cantilever beams resist bending and are designed and intended to bear weight. A common example of a cantilever beam is a balcony. A balcony is supported at only one end with the rest extending over open space. Cantilever beams are generally easy to install, lightweight, and can be used in a variety of structures. They also come with various disadvantages such as cantilever beams are unable to support axial loads, and the size of these beams is limited by large deflections. An axial load is a load where the force is acting on an object parallel to its axis of ration.
To continue reading about structural engineering, please download the whitepaper below.
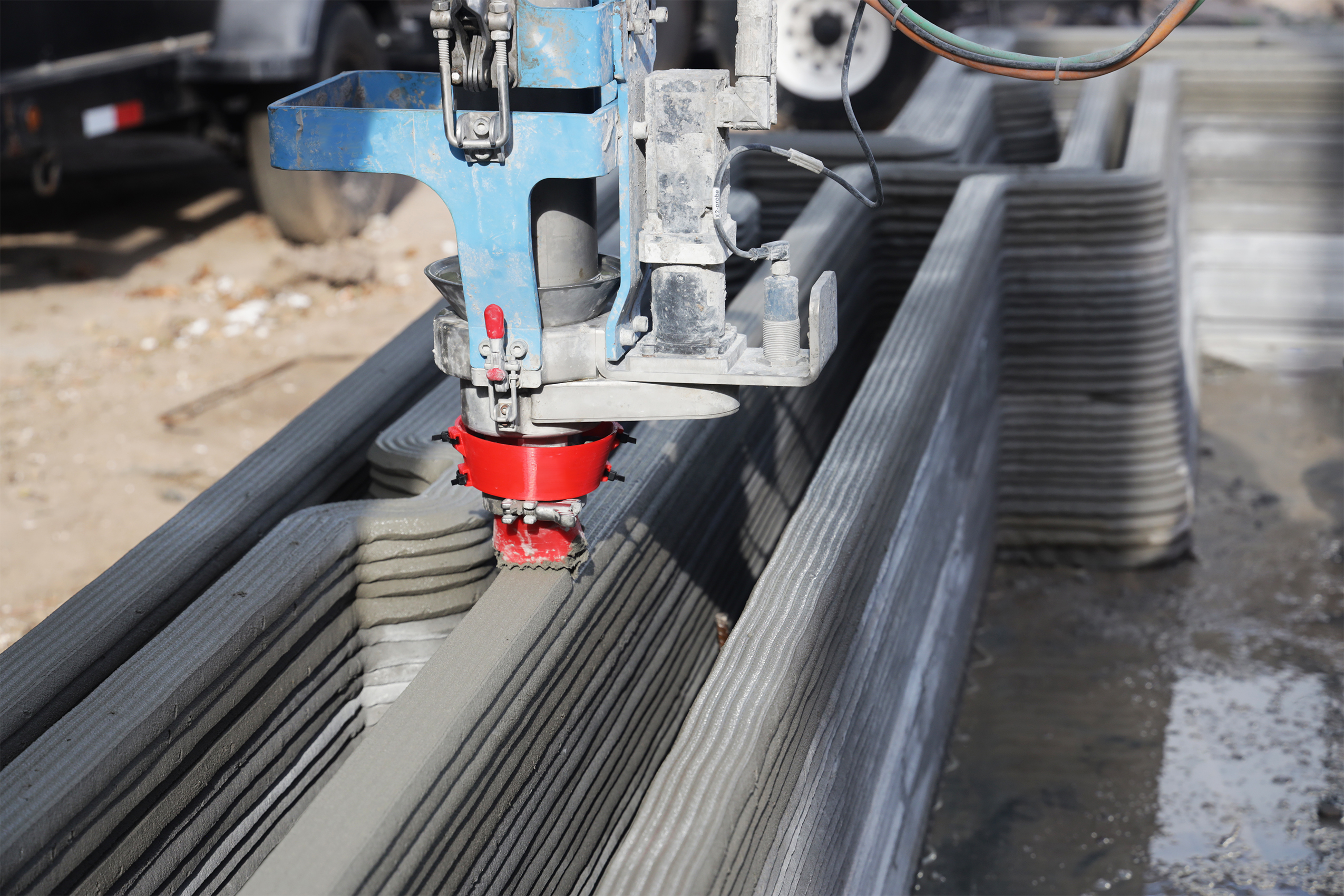
The History of Additive Construction
In the 1914 H.G. Wells novel “The World Set Free”, Wells describes a uranium based continuously combusting explosive. Years later the remarkable similarities discovered between Wells’ fictional device and the atomic bombs invented and deployed during World War II were added to the ever growing list of instances where life imitates art. 3D printing had much the same backstory. In 1945 American author William Fitzgerald Jenkins published his short story “Things Pass By” under the nom de plume Murray Leinster. This story describes a machine that builds things, like houses and ships, using filaments that harden as they set. This is the first documentation of 3D printing as a concept. New developments didn’t occur until decades later. But first, what is 3D printing, and how does it work?
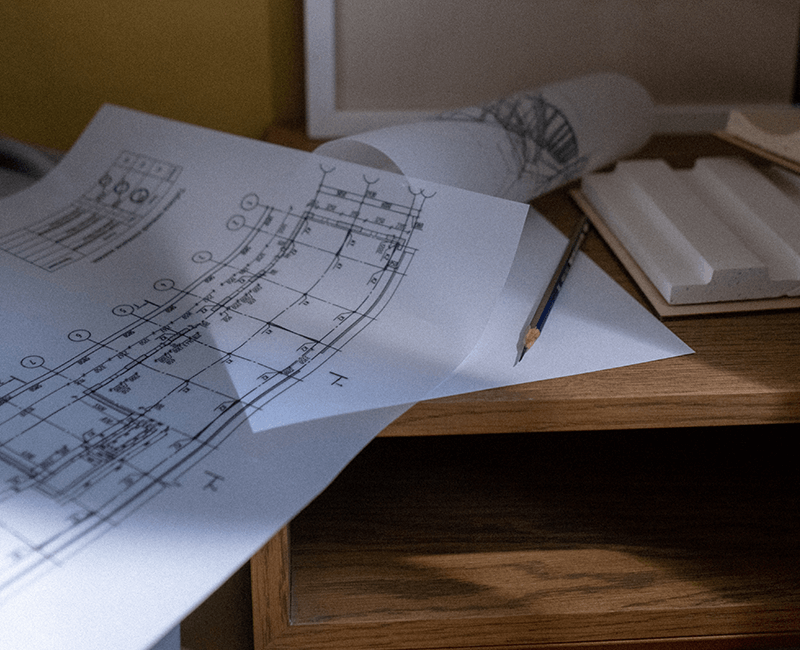
Best Practices in Designing Retail Properties
Investing in real estate is the best way to secure a more consistent long-term return on your capital. Here are some major factors and best practices in designing retail properties you should consider.
Adapting these practices, you can develop commercial retail properties that will ensure you can yield high returns, and your business continues to grow.
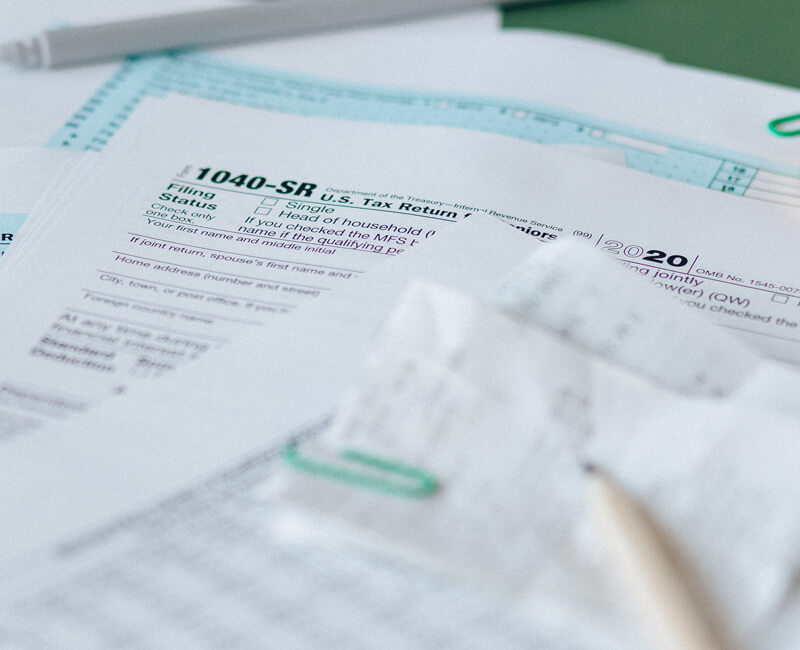
Tax Implications For Construction Contractors
These tax implications for construction contractors are essential, who may face imminent losses during this pandemic. Stay informed during these volatile times to improve your cash flows and profitability. You need to prepare thoroughly for the future and avoid contract losses by speaking to your tax advisers.
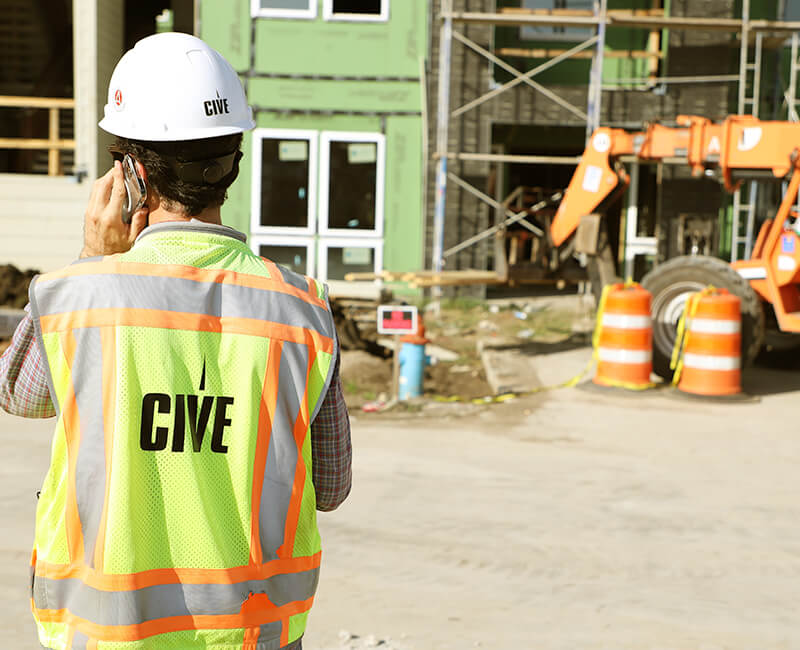
Importance of Leadership in Success of a Construction Project
Leadership, even though sometimes described as a leader of one’s own team, is the essential ingredient for a successful project. Leaders have the unique ability to create the right environment, which in turn facilitates the development of the project and its outcome.
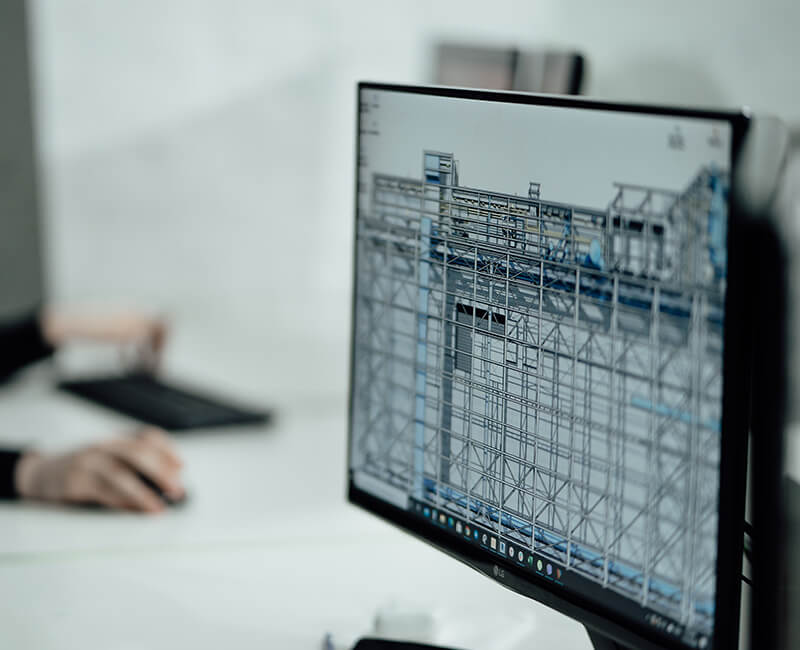
Improving Project Management Outcomes With Technology
Integrating and adapting some of the tactics laid out in this whitepaper can assist managers in improving project management outcomes with technology and help achieve commercial construction results they desire. With proper communication methods, analytics, safety and other resources, developers, contractors and owner will increase their overall project efficiency.
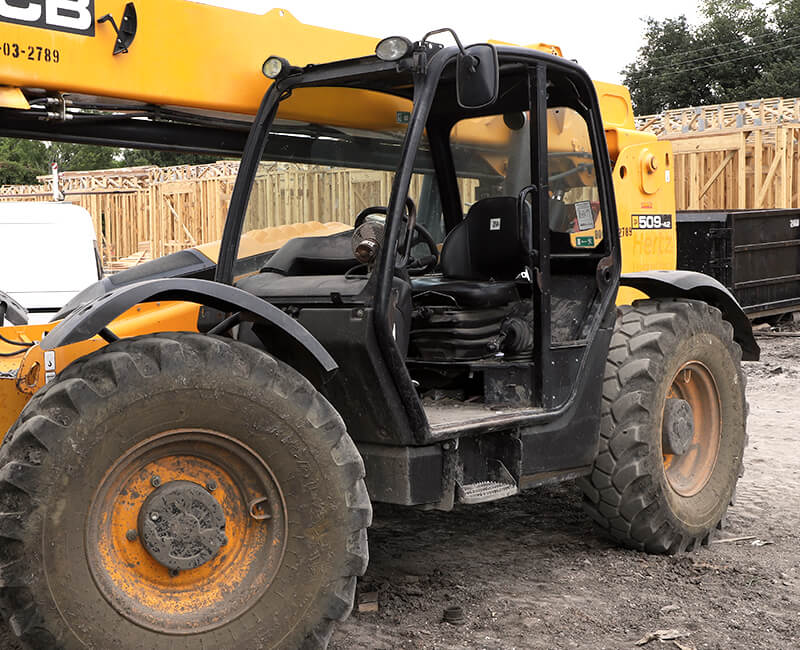
How Construction Companies Can Overcome Scarcity of Labor
A recent study by The Associated General Contractors of America showed that nearly 80 percent of construction companies can’t hire the employees they need due to scarcity of labor. If you experienced a labor shortage or are having a difficult time discovering qualified, skilled workers, you’re not alone. Despite sector growth, companies are still struggling to fill important positions on projects, and as a result, have to miss out on jobs or are forced to delay project schedules.
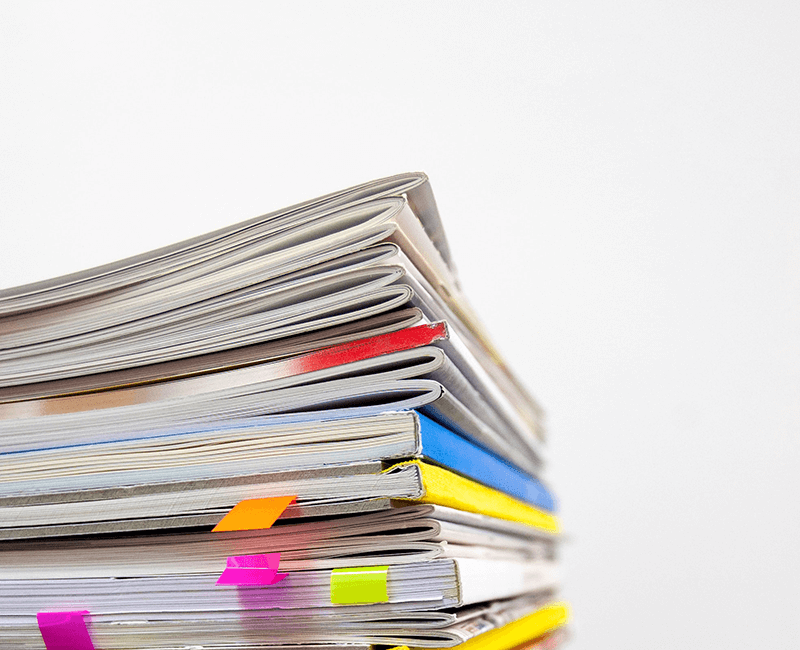
Project Feasibility During an Economic Downturn
Depending on the intensity of an economic downturn, the feasibility of construction projects can be significantly impacted, postponed, or even cancelled. In 2020, the global economy plummeted into a temporary recession after the COVID-19 pandemic deeply affected nearly every industry, disturbing supply chains around the world and forcing businesses to make difficult choices about their operations.
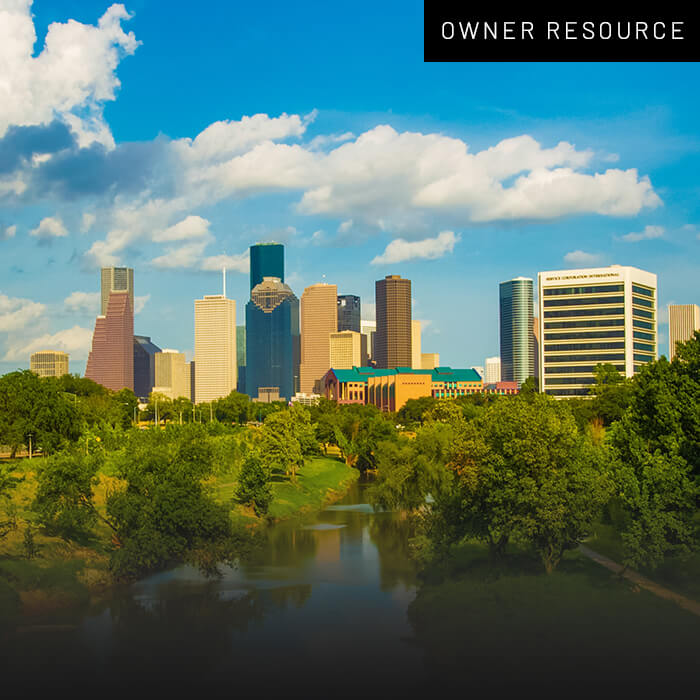
Owning commercial real estate, getting your office space, industrial, retail, multifamily, hospitality, healthcare, or warehouse in Houston demands several investments to be put in place and having reliable infrastructure in the city and surrounding areas. Let’s go over this guide to Houston’s infrastructure.
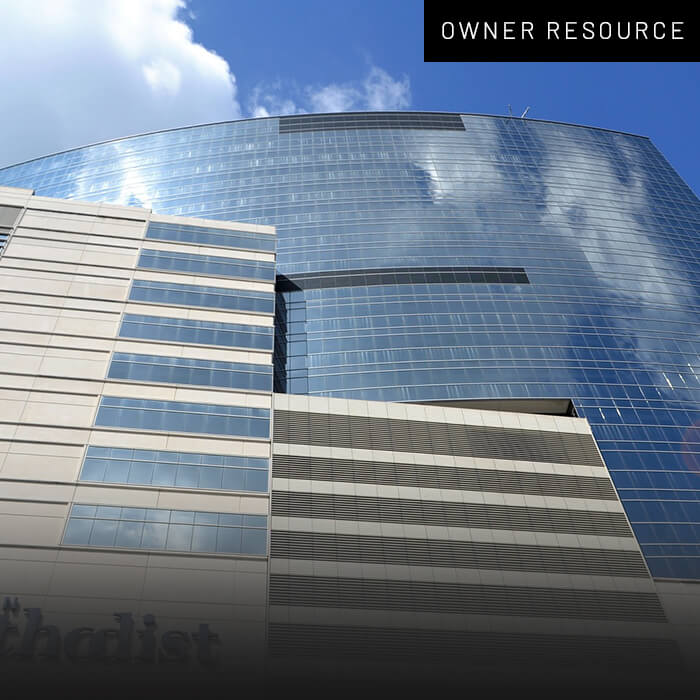
With the pandemic this year, medical facilities, hospitals, and clinics have been a big focus. While some health facilities may not be good long-term opportunities, finding value in medical office properties in Texas with financially stable practices and individual clinics, are excellent opportunities for any real estate investor.

Commercial real estate owners require a reputable, cost-efficient, and reliable contractor to provide what they want and require for property development. Here are a few basic questions a Texas commercial real estate developer should ask before choosing the best commercial contractor.
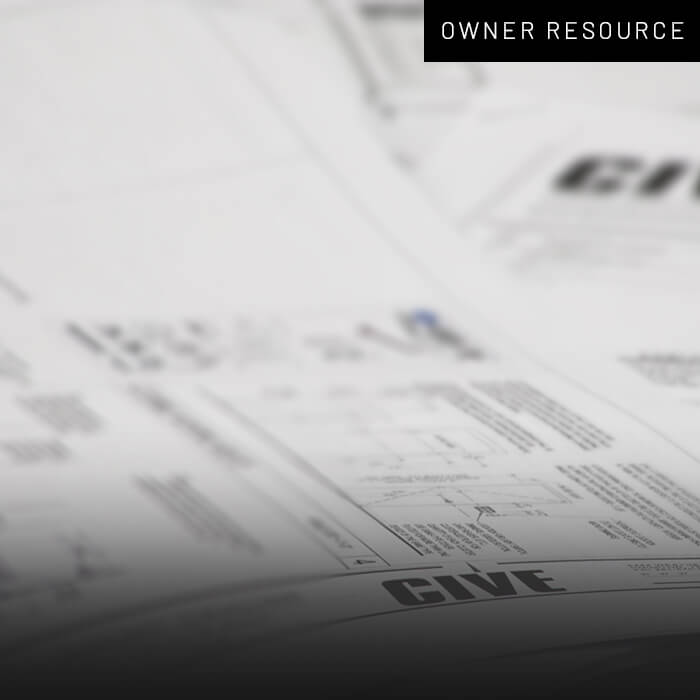
If you are contemplating a new project for commercial construction build, there are a few things to keep in mind prior to getting started. A few items include the designs, plans, timetable, and all the financial estimates. These are important factors to be aware of ahead of time so that you can avoid unnecessary expenses.